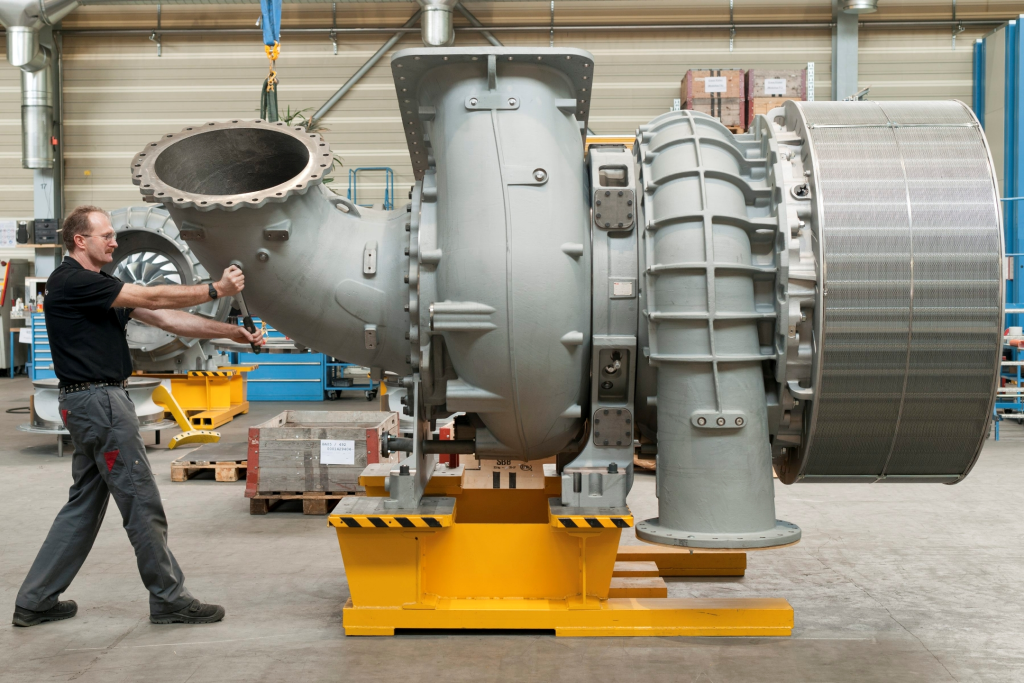
Note: This post first appeared on our old site: TeamUV.org
Turbochargers are a class of superchargers that use a turbine and a compressor on the same shaft to increase the density of the intake air in an engine. Turbochargers come in all sizes and applications, for example: the turbocharger pictured above is for large marine vehicles, while the turbochargers that this article will be focused towards are the much smaller ones that can be found on some automotive engines. As mentioned before, the turbocharger increases the density of the air intake; this is generally accomplished by using the engine’s exhaust gases to spin a turbine which is connected by a shaft to a compressor which takes air from the environment and compresses it prior to feeding it into the engine. Why might one want to do this?
Now, to discuss some of the engineering analysis considerations associated with automotive turbochargers. Within the field of fluid mechanics, most of the considerations are energy related, such as: you must consider any pressure drop across the inlet (think an air filter), the pump work (power required to drive the turbocharger), obstructions to internal fluid flow (major losses associated with components in the flow path or minor losses associated with the changing geometry of the tubes – bends, curves, etc.), exit flow (does it pass through a nozzle, is it directly ducted to the engine intake, is there an expansion fitting), and any additional technologies at play such as intercooling).
From the standpoint of mechanics of materials, one interesting thing to consider would be the shaft inertial effects. What this refers to is the fact that the shaft has mass and that mass is spinning; the revolution of the shaft mass and mass of connected components puts cyclical stresses on the shaft which can lead to premature failure if the shaft is not designed properly.
Lastly, we can look at the turbocharger from the standpoint of control systems engineering: you may want to be able to vary the compressor speed in order to provide variable exit air density to provide for different ranges of engine speeds or to account for changes in elevation/altitude (this would mostly apply to airplane turbochargers), different climates, and so on.
Ultimately, turbochargers provide an excellent example of just how complicated any given system may be from an engineering standpoint as the above text hopefully displays; however, this is not the only purpose of this post, this post also aims to show some aspects of the thought process of an engineer and how truly many ways any given problem can be looked at (and how fascinating the options are)!
can turbine accept ammonia vapors and in place of compressor a generator fitted will work to produce electrical energy ?
Sorry for the late reply, I hope this information was not time-sensitive.
Within the context of an automotive turbocharger, the system you describe does not make much sense; however, if you are asking in a more general way if it is possible to generate electricity by using Ammonia vapors as a working fluid in the turbine for a thermodynamic cycle, the answer is yes. But not necessarily easily.
This type of system is at the root of many current research initiatives regarding closed-cycle OTEC (Ocean Thermal Energy Conversion), in which Ammonia is used as a working fluid in a thermodynamic system (usually based on the Rankine Cycle) to generate electricity. The simple, ideal Rankine Cycle essentially takes a working fluid (in this case Ammonia), boils it to produce a gaseous fluid (the Ammonia vapors), which then pass through a turbine in which it expands, producing energy (power production in the generator, with energy and pressure drop), then passes the working fluid through a condenser (the fluid has now lost much of its energy to the turbine) where it is turned back to liquid form, then passes the liquid to a pump (once again adding energy and pressure, which is much easier to do with a liquid) which feeds it back to the boiler to re-start the process.
In OTEC closed cycles, two types of heat exchangers are used: firstly, cold seawater from the depths is run in pipes next to the Ammonia pipes to accomplish the condensation process, then secondly warmer shallow water is boiled and run alongside the Ammonia pipes for the vaporization process in the boiler. This allows the full cycle to be self contained with the exception of the power input to the pump. Clearly the temperature differences between deep and shallow water are not as large as would be ideal, so maximum realizable power can be quite small, but every day these systems are becoming more efficient and are currently seen as one of the biggest focuses for growth in ocean energy production and the provision of alternative energy production.
Hope that helped. There are other systems that used Ammonia vapors for basic thermodynamic cycles for energy production; however, this is one of the most significant with regards to contemporary (current) engineering industry trends, not to mention one of the most exciting and interesting uses. You can read more on OTEC here, here, and here.