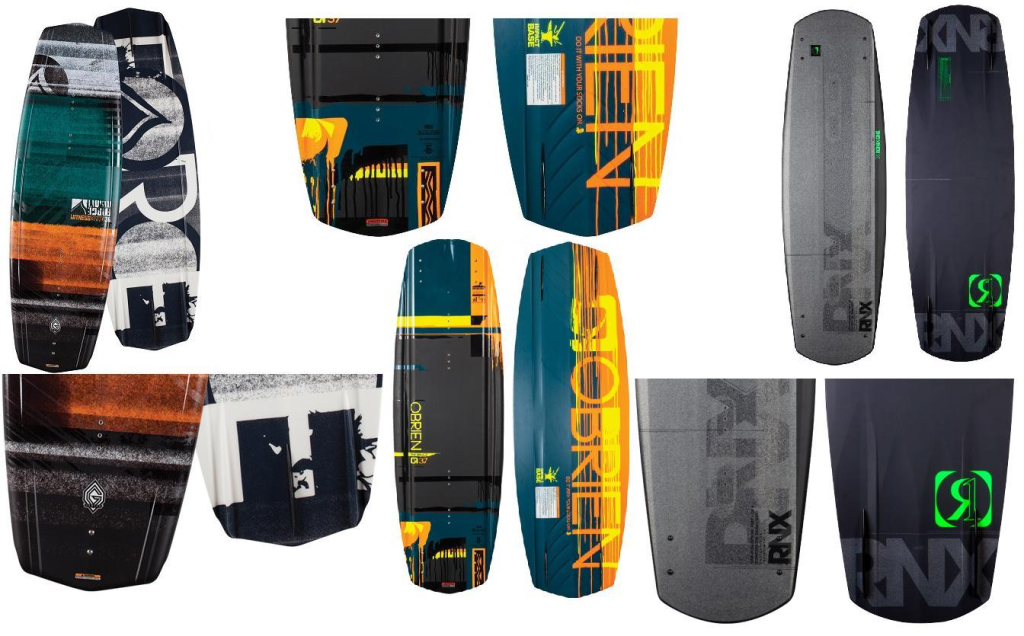
Due to some family affairs I had to attend to, I was unable to finalize my planned post for today and so instead will be re-posting an oldie, but a goody. The following post was originally published by me on our old site (TeamUV.org) in September 2014, and was a personal favorite of mine, that I had a lot of fun writing and I hope that you will all enjoy reading it and learning a little bit about what it takes to design a good wakeboard!
Wakeboarding is one of my favorite sports and provides a fascinating study in fluid mechanics and materials science (in addition to many other fields of engineering). It would be quite interesting to serve as a design engineer within the framework of a wakeboard company as I believe that there are quite a few features of today’s wakeboards that could be vastly improved; in many cases, engineers are currently making these improvements to the end of providing unheard of complexity in what many see as simply a slab of plastic/wood.
As can be seen in the above picture, many wakeboards make use of intricate channeling, “concaves”, and strategically sized, shaped, and placed fins. The use of these features helps to create boards that are as much art pieces as they are sports equipment, but the use of these features penetrates far deeper than the superficial appearance of the board; each of these features is used to create different fluid effects in order to manipulate the board’s performance and functionality.
The fins act to provide the tracking characteristics of the board by breaking the surface tension of the water, essentially digging into the water in order to provide sufficient “traction” (think the treads on the tires of your car). If one was to remove the fin from the tail end of the wakeboard, it is immediately noticeable and acts to make the ride “squirrely”, making it difficult to keep the tail of the board seated in the water in a steady/stable fashion (think driving a car that has balding/smoothed tires). The channels act as extended fins, extending the “traction” provided at the tail in order to provide better edge tracking capabilities (for cutting on your heel-side or toe-side edge). Lastly, the concaves actually work to increase what is essentially the hydrodynamic lift of the board. In doing so, these concaves can act to elevate the tail, midsection, and/or the nose of the board, depending on the placement, sizing, shape, and orientation of the concaves, allowing the board to sit higher in the water (thus reducing drag through reduction of the waterplane area, or cross-sectional area at the waterline, as well as shifting the weight of the rider for a more comfortable ride). These concaves can even be shaped in a way so as to accelerate the flow when cutting in towards the wake, effectively giving you a speed boost right before you hit the wake.
Often times engineers will strategically combine all of these effects into one board, providing for some pretty awesome effects within the fluid flow and variety in board design that is nothing short of phenomenal. If I were to be a part of a R&D (research & development) team within the context of a wakeboard design firm, I would target the increased use of concaves in order to provide more hydrodynamic lift in strategic areas along the heel-side and toe-side edges in order to provide more wake-side pop, allowing the rider to get more air. Furthermore, it is conceivable that if designed properly, the concaves (combined with channels) could provide enough pop to, much like the hybrid rocker, mitigate the dramatic difference that currently exists between 3-stage rockers and continuous rockers as shown below (3-stage is used to get more pop out of the board, much like the lips on a skateboard, while continuous is used to provide smoother maneuvering).
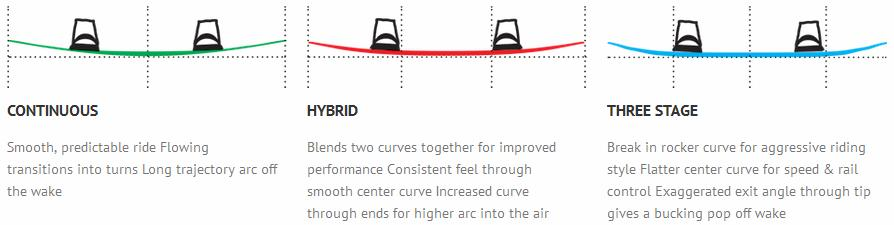
Photo Credit: LiquidForce.com
Materials science plays a huge role in wakeboard design; boards have to be designed to be buoyant, smooth, stiff (yet capable of storing/releasing large amounts of energy), durable, resistant to moisture absorption, strong, lightweight, UV resistant, and much much more. In order to cater to this broad list of demands, wakeboard designers use composite materials in order to take advantage of the properties of multiple individual materials by combining them strategically. A relatively simple wakeboard construction is shown below (many boards have over twice this many layers!). A major focus for future board development with regards to composite materials would have to be the use of materials with higher specific strength (essentially strength per unit weight) to provide lighter weight boards (after all, binding/boots already weigh enough without having to worry about board weight) as well as materials with better elastic response properties for better cushioning when coming down from tricks (which would both relieve impact as well as decrease the chance of the board sinking enough to bury the nose, leading to a painful face-plant). Taking better advantage of the elastic response of the materials could also lead to a more comfortable ride in choppy water (being dragged at 20-25 knots through a wind-whipped lake doesn’t exactly feel good…each one of those little ripples feels like hitting a speed bump when you’re moving upwards of 20 mph!).
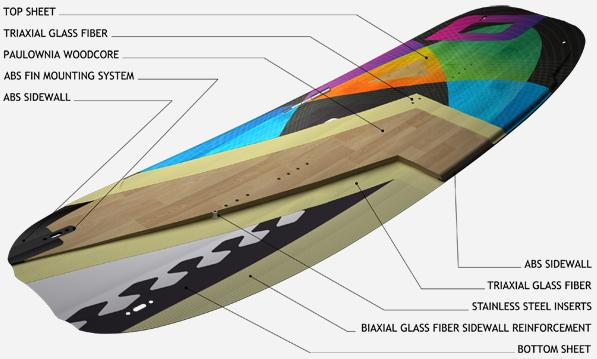
Lastly it is worth noting how it never ceases to amaze me how poorly many bindings/boots hold up in the sun. Unfortunately, in order to save money, many companies manufacture their boots/bindings with thermoplastics or thermoplastic elastomers, which readily transition to a viscous state in the sun (in essence they melt into a sticky, rubbery substance!). Many people may have also experienced this material flaw in cheap bike handlebar grips, leading to the unpleasant transfer of rubbery residue to your hands. Bindings/boots can become sticky after being used or sitting in the sun for just a few months, leading to the need to buy new boots/bindings that use leather and other expensive materials, which cause the price tag of the boots to skyrocket! All I am saying is that if I were to design wakeboard boots, I would use thermosets,or typical thermosetting elastomers, or at least make sure that the degradation temperature of the thermoplastic or thermoplastic elastomer would be high enough so that the boots function without turning into a sticky mess!