Have you ever heard of Shape Memory Materials (SMM)? Neither had I, so I decided to do a little research on the topic. Here is what I found.
The discovery of SMMs can be dated back to the early 1950’s and they have been extensively studied since. There are many types of SMMs in the world so to keep things practical, I will mainly focus on Shape Memory Alloys (SMAs). SMAs are the closest thing to magic in world of metallurgy. Essentially the material can be deformed unrecognizably and then it can return to its original “parent” shape by changing the temperature or by stressing the material. Now before you start lighting your torches and grabbing your pitchforks, this is not witchcraft. Let me assure you there is a scientific explanation that can be found in the microstructure of the material.
The key to their wizardry is in controlling the solid-state phase of the SMA. Nitinol is the most common SMA and is an alloy of Nickel and Titanium (Ni-Ti). The two phases of interest that produce the shape memory effect are Martensite and Austenite. WARNING: Do not confuse the phases of Martensite and Austenite that occur in the Ni-Ti system with those that occur in the Fe-C (steel) system as they do not behave the same. Gibbs Free Energy, as you may remember, is a thermodynamic tool that you used in your high school chemistry class to determine whether a chemical reaction will spontaneously occur or not. Gibbs Free Energy is also used in physical metallurgy and can determine whether or not a certain phase will be favored.
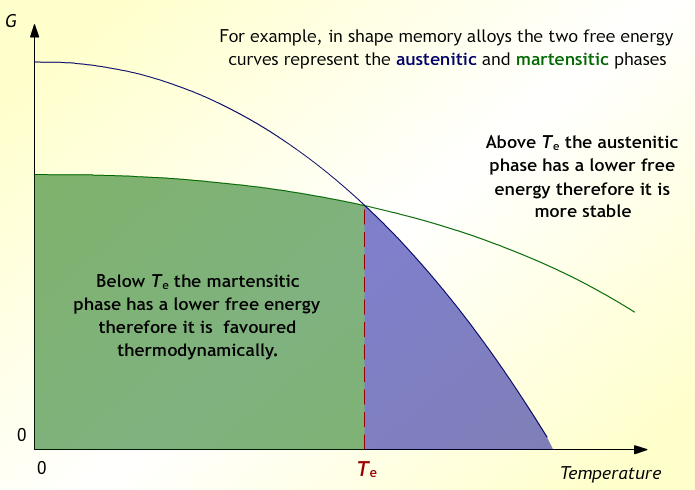
However there is not a certain temperature that causes a phase change entirely, there are a range of temperatures that allow for the nucleation of a new phase within another and they differ when heating to transform the Martensite to Austenite and when cooling from Austenite to Martensite. In the case of SMAs this is called transformation temperature hysteresis.
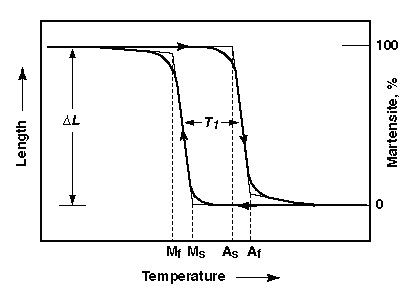
There is also the phenomenon called pseudo-elasticity or superelasticity in which a similar phase transformation cycle occurs except without a change of temperature but instead a change in stress. Now in order to get a SMA to “memorize” its shape, it must be “trained”. Now exactly how this is done is a trade secret depending on the manufacturer but essentially the process is a thermo-mechanical treatment that the material must undergo to have a preferred recovery shape. The material is constrained in a certain shape and raised to a certain temperature well above the Austenite transformation temperature and then cooled to a temperature below the Martensite transformation temperature. During the thermo-mechanical cycle the lattice structure rearranges itself in many different ways and the atoms arrange themselves in a pleasing way (twin boundaries) that lowers the elastic strain energy during the phase transformations. So what that last sentence means is that the energy required to go back to the parent shape is minimized and therefore the material is predisposed to returning to that shape when changing phases. The parent shape is “memorized”. Now when the material is deformed and then heated above the final Austenite temperature, the material will reconfigure to the parent phase and shape magically!

There are many interesting uses for SMAs and more recently a team of German engineers are using SMAs to create a new kind of lightweight prosthetic arm that uses Nitinol fibers as tendons and muscles to manipulate the arm. Amazing!
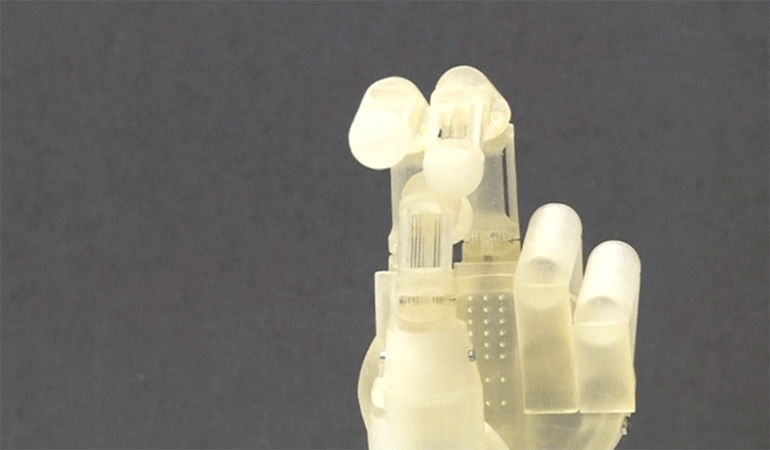